Membrane Bioreactor (MBR)
A Membrane Bioreactor (MBR) is an advanced wastewater treatment technology that combines biological treatment with membrane filtration. MBRs have gained popularity for their ability to produce high-quality effluent by effectively separating solids from treated water.
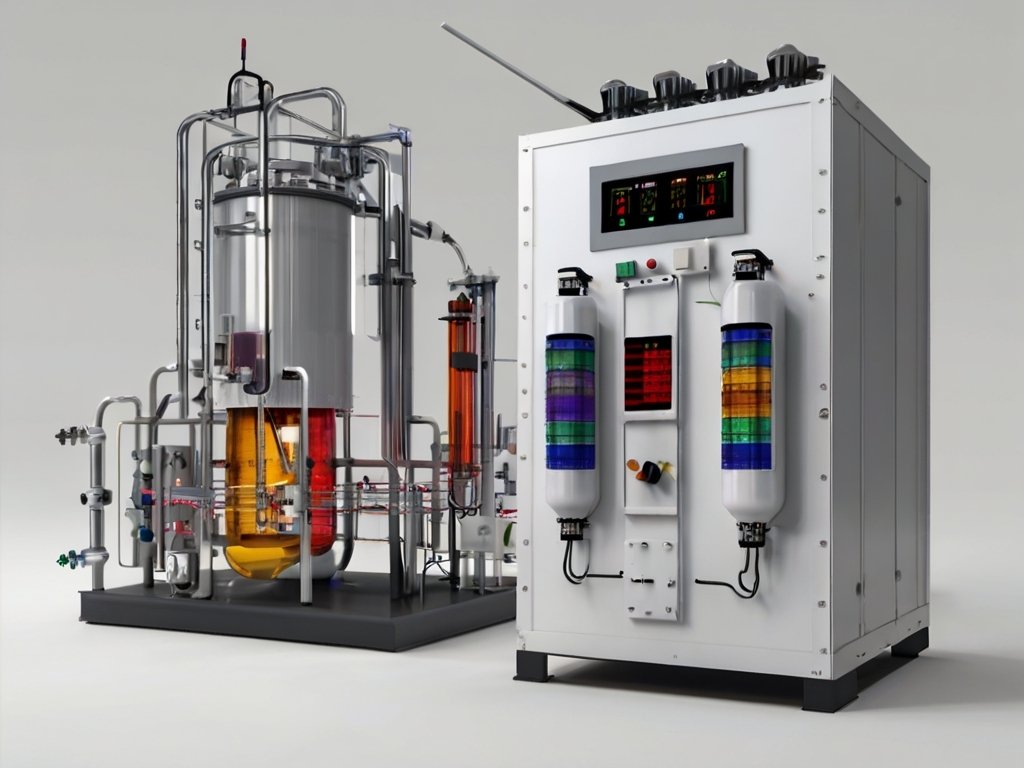
Key Components and Operation
Bioreactor Tank:
The bioreactor in an MBR serves as the primary treatment unit, where microorganisms break down organic matter through biological processes, similar to traditional activated sludge systems.
Membrane Filtration:
MBRs employ membrane filtration, typically using ultrafiltration (UF) or microfiltration (MF) membranes. These membranes have small pores that effectively separate suspended solids, bacteria, and other impurities from the treated water.
Aeration System:
Aeration is crucial for providing oxygen to support the growth of aerobic
microorganisms in the bioreactor. This process enhances the breakdown of
organic pollutants.
Membrane Modules:
Membrane modules are arranged within the bioreactor, forming a barrier that
retains biomass and solids while allowing clear water to pass through. The
membrane modules can be submerged in the mixed liquor or placed outside
the bioreactor.
Pump System:
A pump system is used to maintain the required flow of mixed liquor through
the membrane modules. This helps prevent fouling and clogging of the
membranes.
Advantages of Membrane Bioreactors
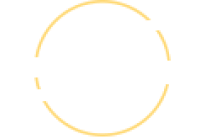
High-Quality Effluent
MBRs produce treated water of exceptional quality due to the efficient removal of solids, bacteria, and pathogens by the membrane filtration.
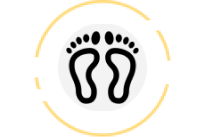
Reduced Footprint
MBRs often have a smaller footprint compared to conventional wastewater treatment systems because they eliminate the need for a separate settling tank. This is particularly beneficial in situations with limited space.
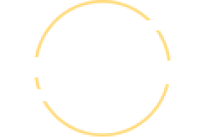
Process Intensification
The combination of biological treatment and membrane filtration intensifies the treatment process, allowing for higher concentrations of biomass and more effective removal of contaminants.

Flexibility and Scalability
MBRs are flexible and can be applied to various scales, from small decentralized systems to large municipal or industrial wastewater treatment plants.
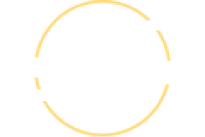
Potential for Water Reuse
The high-quality effluent produced by MBRs is suitable for various non- potable water reuse applications, contributing to sustainable water management.
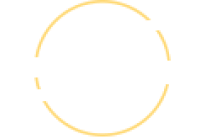
Reduced Sludge Production
MBRs typically produce less sludge than traditional activated sludge systems, leading to reduced sludge handling and disposal requirements.
Challenges and Considerations
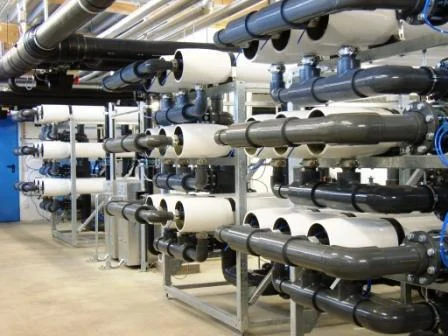
Membrane Fouling
Membrane fouling is a common challenge in MBRs, where particles and
microorganisms accumulate on the membrane surface. Regular cleaning and
maintenance are essential to prevent performance decline.
Energy Consumption
The operation of membrane modules and aeration systems in MBRs requires
energy. Strategies to optimize energy efficiency are crucial for sustainable
operation.
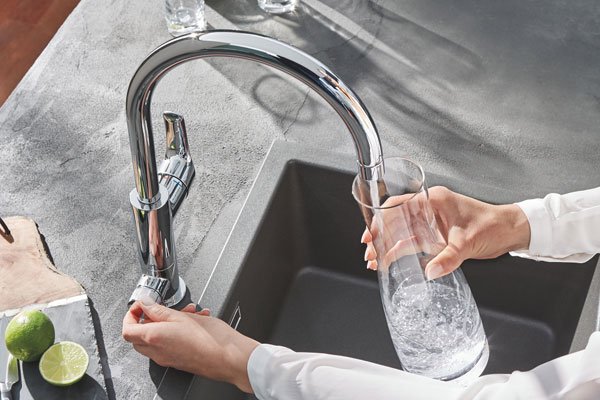
Applications
Municipal Wastewater Treatment
MBRs are widely used in municipal wastewater treatment plants, offering high-quality effluent suitable for discharge or water reuse.
01.
Industrial Wastewater Treatment
Various industries, such as food and beverage, pharmaceuticals, and petrochemicals, employ MBR technology for the effective treatment of
industrial effluents.
02.
Decentralized Systems
MBRs are suitable for decentralized or remote systems where space is limited or stringent effluent quality is required.